The Ultimate Guide to Rapid Prototype Plastic in Modern Business
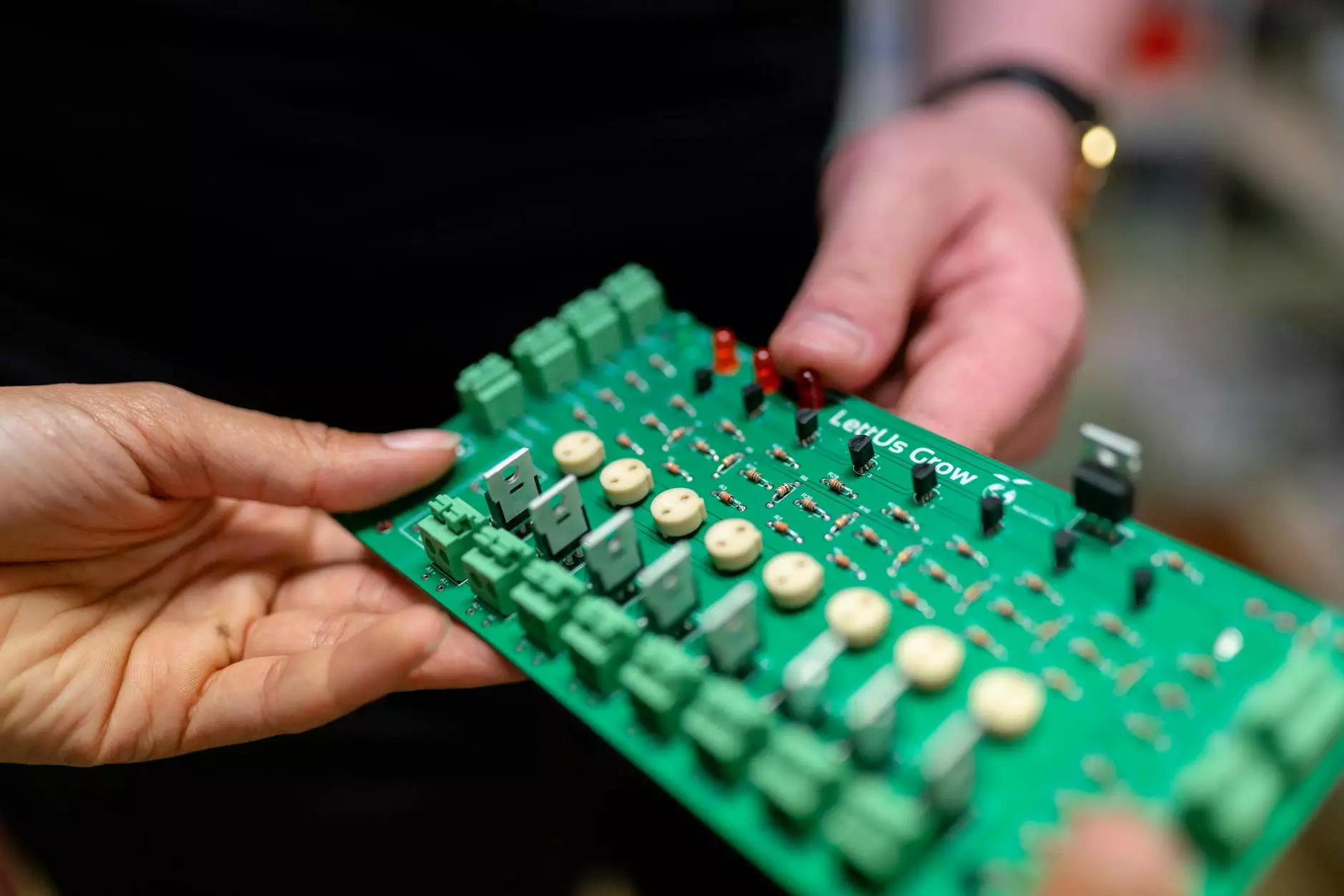
In the ever-evolving world of manufacturing, rapid prototype plastic plays a pivotal role in how businesses innovate and bring their products to market. From design to production, this technology provides manufacturers with the tools they need to create high-quality prototypes efficiently and cost-effectively. In this comprehensive article, we will delve into the significance of rapid prototype plastic, its applications in various industries, and how it enhances the capabilities of metal fabricators like those at Deep Mould.
What is Rapid Prototyping?
Rapid prototyping refers to the processes used to quickly fabricate a scale model or a functional part using three-dimensional computer-aided design (CAD) data. It is a methodology that promotes swift iterations and testing, crucial for speeding up the development process in manufacturing and design.
The Materials: Understanding Rapid Prototype Plastic
Rapid prototyping primarily utilizes various types of plastics, each selected based on the desired properties and specific applications. Here are some commonly used rapid prototype plastics:
- ABS (Acrylonitrile Butadiene Styrene) - Known for its durability and strength, ABS is often used for models that require impact resistance and a good surface finish.
- PLA (Polylactic Acid) - A biodegradable plastic derived from renewable resources. It's easy to work with and is often used for visual prototypes.
- PETG (Polyethylene Terephthalate Glycol) - Offers flexibility and is ideal for functional prototypes and applications requiring chemical resistance.
- Nylon - Renowned for its strength and flexibility, making it suitable for parts that will undergo considerable wear and tear.
Advantages of Using Rapid Prototype Plastic
Utilizing rapid prototype plastic offers several advantages for businesses:
1. Speed and Efficiency
Time is of the essence in today's fast-paced market. With rapid prototyping, designers and engineers can produce models quickly, allowing for faster iterations and development cycles, which is essential to stay competitive.
2. Cost-Effectiveness
By testing ideas with rapid prototypes, businesses can avoid costly mistakes in the later stages of production. The ability to iterate designs before mass production results in significant cost savings.
3. Enhanced Design Flexibility
Rapid prototyping allows for design changes to be made spontaneously. This flexibility is imperative, especially when feedback from potential customers or testing indicates a need for adjustments.
4. Increased Product Quality
With the opportunity to test and refine prototypes thoroughly, companies can ensure that the final products meet high standards of quality, leading to greater customer satisfaction.
Key Applications of Rapid Prototype Plastic
The ability to create efficient prototypes opens opportunities across various industries:
Aerospace
In the aerospace sector, where precision and safety are paramount, rapid prototyping enables engineers to test components for performance and aerodynamics, significantly reducing the risks associated with new designs.
Medical Devices
The medical industry relies on rapid prototyping for creating devices that meet regulatory requirements, ensuring functionality and safety, and, importantly, quick adaptation to changes in consumer needs.
Automotive
From conceptual designs to production parts, the automotive industry employs rapid prototyping to create parts that are not only functional but also capable of undergoing rigorous testing before full-scale production.
Consumer Products
In consumer goods, rapid prototyping has revolutionized how businesses gather consumer feedback, allowing rapid changes to meet customer preferences effectively.
The Role of Metal Fabricators in Rapid Prototyping
Metal fabricators, such as those at Deep Mould, play a critical role in the landscape of rapid prototyping by offering services like:
1. Tool and Die Creation
Metal fabrication is essential in producing tooling for prototypes. This includes molds and dies that are necessary for the mass production of various plastic parts.
2. Structural Components
For many prototypes, having a combination of metal and plastic components is vital. Metal fabricators can create the necessary structural support that ensures prototypes maintain integrity during testing.
3. Advanced Technologies
Using cutting-edge technologies, metal fabricators can integrate features into prototypes that might be difficult to achieve through traditional means. This ensures innovative and effective product development.
Future of Rapid Prototyping and Plastic Technologies
The future of rapid prototype plastic is bright, with advancements in technologies such as:
1. 3D Printing Innovations
As 3D printing technologies advance, the scope of materials and processes available will continue to grow. This will lead to high-quality prototypes that can be produced in even shorter time frames.
2. Sustainable Practices
With increasing concern for the environment, the rise of sustainable rapid prototype plastics that are biodegradable or made from recycled materials is gaining momentum.
3. Integration of AI and Machine Learning
Leveraging AI for design optimization and predictive modeling could streamline prototyping processes, making them more efficient and cost-effective.
Conclusion
In conclusion, the use of rapid prototype plastic is reshaping how businesses approach product design and manufacturing. Companies like Deep Mould embody the future of metal fabrication, successfully integrating rapid prototyping into their operations to enhance productivity and innovate new products. As technology evolves, embracing these advancements will allow businesses to remain competitive in an increasingly complex marketplace.
Embracing rapid prototyping is not just a trend—it's a commitment to quality, efficiency, and sustainable practices that will drive modern business forward. With the right strategies and partnerships, the potential for innovation through rapid prototype plastic is limitless.