Plastic Injection Molds for Sale: Revolutionizing Manufacturing for Metal Fabricators
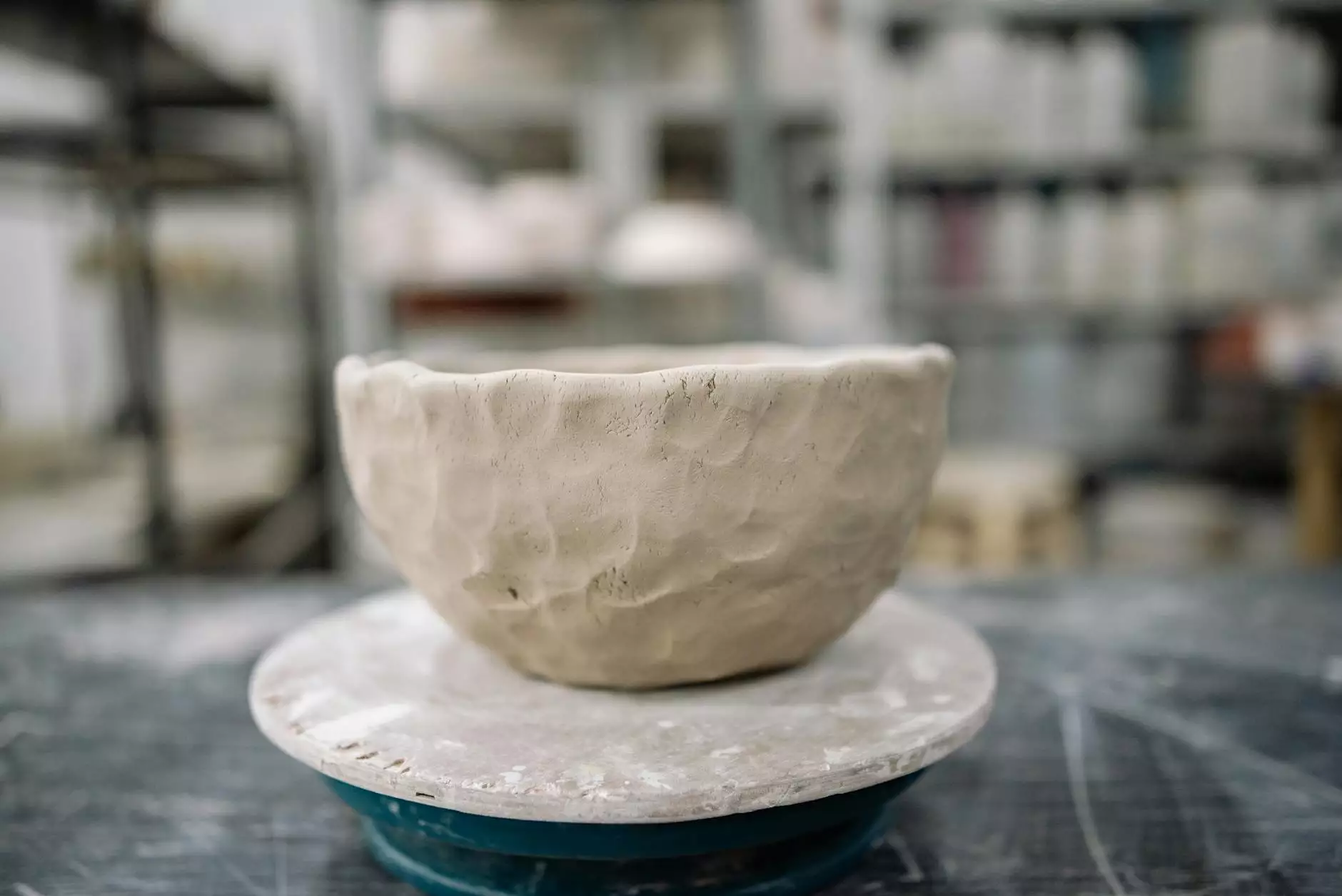
In today's rapidly evolving industrial landscape, the demand for high-quality, durable, and efficient manufacturing solutions is paramount. Among these solutions, plastic injection molds play a crucial role in ensuring precision and consistency in production. If you are a metal fabricator or an industrial business owner, you are likely on the lookout for reliable plastic injection molds for sale. This comprehensive guide will delve into the benefits, types, and considerations when purchasing plastic injection molds, especially from deepmould.net.
Understanding Plastic Injection Molding
Plastic injection molding is a manufacturing process used to produce parts by injecting molten material into a mold. This technique is favored across multiple industries due to its ability to create complex shapes, reduce waste, and produce high volumes of parts. The process involves several key steps:
- Material Selection: Common materials include thermoplastics and thermosetting plastics.
- Mold Design: Custom molds are designed to meet specific requirements.
- Injection Process: The selected material is heated to a molten state and injected into the mold.
- Cooling and Ejection: Once cooled, the finished part is ejected from the mold.
The Importance of Quality in Plastic Injection Molds
When it comes to purchasing plastic injection molds, quality cannot be overstated. High-quality molds are essential for:
- Precision: Accurate molds lead to consistently produced parts, minimizing defects.
- Durability: High-grade materials enhance the mold's lifespan, reducing replacement costs.
- Efficiency: Well-designed molds optimize the injection process, improving overall productivity.
Key Factors to Consider When Buying Plastic Injection Molds
Buying plastic injection molds for sale involves several critical considerations to ensure you make an informed decision:
1. Material Quality
Choose molds made from high-quality steel or aluminum. The choice between steel and aluminum depends on factors like production volume and part complexity. Steel molds are more durable, while aluminum molds are lighter and ideal for low to medium run productions.
2. Mold Design
The design of the mold is crucial for efficiency. Partner with a supplier who offers custom design services to meet your specific needs. A well-thought-out design can reduce cycle times and production costs.
3. Supplier Reputation
When searching for plastic injection molds for sale, consider the reputation of the supplier. Check reviews and testimonials to ensure the supplier delivers quality products and excellent customer service.
4. Cost Considerations
Pricing can vary significantly based on several factors, including material, design complexity, and supplier. It's essential to balance cost with quality to ensure you get the best value for your investment. Remember that the cheapest option might result in higher long-term costs due to repairs and replacements.
5. Lead Time
Timeliness is crucial in manufacturing. Discuss lead times with potential suppliers to ensure they can meet your production schedules. Delays can result in increased costs and lost opportunities.
The Benefits of Plastic Injection Molding for Metal Fabricators
For metal fabricators, using plastic injection molds can offer numerous benefits:
- Versatility: Molding can be used for a wide range of applications, from automotive parts to consumer products.
- Cost-Effectiveness: High production volumes reduce the cost per unit significantly, enhancing profitability.
- Eco-Friendly: The injection molding process can be optimized to reduce waste, making it a more sustainable option.
Conclusion
Investing in plastic injection molds for sale is a strategic decision that can enhance production efficiency and product quality for metal fabricators. By focusing on the quality of molds, exploring reliable suppliers like deepmould.net, and understanding the nuances of the injection molding process, businesses can thrive in a competitive landscape. This comprehensive approach ensures that you are not just purchasing a product, but are also investing in the future of your operations.
FAQs About Plastic Injection Molds
1. What are the typical lead times for plastic injection molds?
Lead times can range from a few weeks to several months, depending on the complexity of the design and the supplier's capabilities. Always ask for an estimate before placing an order.
2. Can I use the same mold for different materials?
While some molds can be adapted for multiple materials, it's essential to consider the physical properties of the materials and the design of the mold to ensure compatibility.
3. How do I maintain my plastic injection molds?
Regular maintenance, including cleaning and lubrication, is crucial for preserving the mold's lifespan. Follow the manufacturer's recommendations for best practices.
4. What are the signs that a mold needs replacement?
Common signs include persistent defects in the produced parts, excessive wear and tear, and inability to maintain production rates. Early replacement or refurbishment can save costs in the long run.
5. Are there standard sizes for plastic injection molds?
Molds can be custom-designed to fit specific applications, and while there may be standard sizes for certain industries, many molds will be tailored to the unique requirements of a project.
In summary, understanding the intricacies of plastic injection molds and making well-informed purchases can position your business for success in the manufacturing sector. Explore the vast array of options available and capitalize on the expertise of industry leaders like deepmould.net.